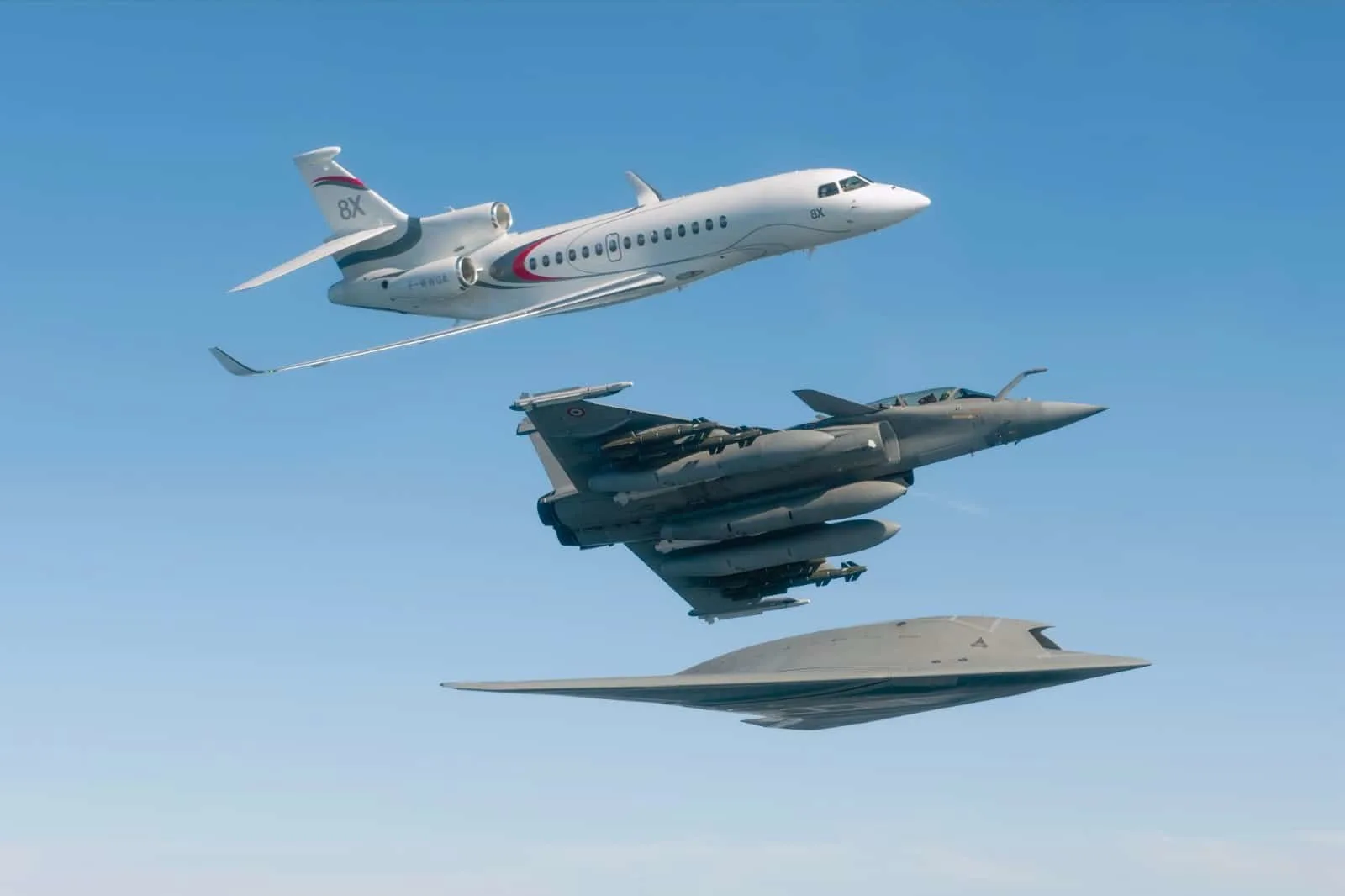
El proyecto MultiFAL (Multifunctional Automation System for Fuselage Assembly Line), que forma parte del programa de innovación Clean Sky 2 respaldado por la UE, es un claro ejemplo de cómo la industria aeroespacial sigue superando los límites de la innovación para reducir su impacto ambiental. Esta iniciativa pionera pretende desarrollar un sistema automatizado de planta para el ensamblaje de carcasas de fuselaje con termoplásticos , que son más resistentes y ligeros que los materiales utilizados tradicionalmente y pueden ayudar a reducir los costes de combustible y las emisiones de CO₂.
Pero ampliar su uso de la fabricación de componentes pequeños a la de algo tan grande como un fuselaje es un gran reto: unir dos carcasas de material compuesto requiere herramientas robóticas muy potentes y especializadas con un avanzado software de control.
The CT Engineering Group, empresa líder en ingeniería a lo largo de todo el ciclo de vida del producto, coordina el proyecto MultiFAL para crear una planta de ensamblaje de este tipo reutilizando las instalaciones y los robots existentes.
En este sentido, CT quiso apoyarse en una plataforma innovadora para respaldar el diseño y las pruebas del sistema de planta automatizada, por lo que implementó la plataforma 3DEXPERIENCE de Dassault Systèmes y su experiencia en soluciones industriales “Engineered to Fly” en la nube para todo el diseño, simulación, gestión de proyectos, visualización de datos de producto y coordinación del proyecto MultiFAL.
Al construir y probar primero la planta en el entorno virtual, en el marco de un proyecto coordinado e integrado, CT ha demostrado que es posible reducir el tiempo de puesta en marcha de los sistemas automatizados de la planta hasta en un 20%. Al mismo tiempo, al conectar el sistema de planta y las interfaces de control de producción, ha mejorado el nivel de detalle en la definición de los pasos de producción detallados necesarios para un montaje satisfactorio del fuselaje termoplástico.
Por otra parte, el modelado virtual de MultiFAL ha permitido reducir los costes de inversión de la planta hasta en un 20% gracias a la modernización, la ampliación de los sistemas de montaje existentes y el uso de la simulación para probar y validar requisitos de construcción complejos, planificación eléctrica y diseño de controladores. Además, gracias a la automatización y el control integrado del sistema, también ha sido posible reducir los costes de montaje entre un 10 y un 30% y reducir el tiempo de inactividad de las máquinas en un 10%.
En proyectos complejos como este, es esencial una estrecha colaboración. De hecho, uno de los objetivos clave ha sido integrar el conjunto de requisitos de todas las partes interesadas en el desarrollo del sistema de producción y, en este sentido, la plataforma 3DEXPERIENCE ha conseguido mejorar la coordinación entre todos los colaboradores: diseñadores, gestores, socios y proveedores externos.